Material 1.2311
Cold work tool steel
1.2311 is a low-sulfur tool steel. This steel can be polished and etched well. Usually this material is supplied in quenched and tempered form and is often not heat treated again .1.2311 material can be through hardened and tempered and therefore has uniform strength. Due to its properties, 1.2311 has a wide range of applications. It is frequently used, for example, in general mechanical engineering.
Material 1.2311 - tool steel for many applications
Steel is one of the most important construction materials worldwide. Depending on the intended use, there is a corresponding steel grade. Detailed, desired properties can be directly matched to product requirements by special processing techniques. We at BASEDO STEEL offer you around 20 material groups ranging from free-cutting steel to tool steel for hot work. From the group of tool steels for cold work we present the material 1.2311.
What does tool steel for cold work mean?
Basically, this steel grade is well suited for tools for which surface temperatures up to a maximum of 200 degrees Celsius are current.
Material 1.2311 is a low-sulfur tool steel. It is easy to etch, polish and through-temper. This material has uniform strength, good toughness, high hardness and is easy to machine. The hardness value, i.e. practical mechanical properties of the quenched and tempered tool steel 1.2311, is 280-325 HB (= Brinell hardness). When heat treated, the material 1.2311 shows little dimensional change.
The material 1.2311 with the international designation AISI P20 is a standard plastic mold steel. Its density is 7.85 kg per cubic decimeter. The material is especially suitable for plastic molds, has high dimensional stability and is particularly suitable for polishing.
Chemical analysis of 1.2311 yields the following mass fractions in percent :
Chromium (Cr) 1.80 - 2.10, Carbon (C) 0.35 - 0.45, Manganese (Mn) 1.30 - 1.60, Molybdenum (Mo) 0.15 - 0.25, Silicon (Si) 0.20 - 0.40.
The material has good weldability and is characterized by good machinability and grainability. The working hardness is 32 - 50 HRC (Rockwell C hardness).
There are many applications for material 1.2311
In addition to its use for plastic and die casting molds, material 1.2311 is also used for various other devices. Material 1.2311 is also used for mold frames, base plates, die inserts and die holders as well as various parts in general mechanical engineering. Other applications include body parts, bending strips, hydroforming tools, tube presses, tool holders and intermediate sleeves.
Delivery condition of material 1.2311 & treatment options
We supply material 1.2311 in prehardened and tempered condition. In addition to the advantageous properties already mentioned, this also means good corrosion and wear resistance. Further heat treatment is therefore usually not necessary.
The following instructions apply to appropriate heat treatments: For soft annealing we recommend temperatures of 710 - 740 degrees Celsius. This should be followed by slow cooling in the furnace. If nitriding is planned, we recommend stress relieving at 580 degrees beforehand.
After hard chrome plating (which increases wear resistance and corrosion resistance), you should anneal the corresponding tool for about three to four hours at 180 degrees. Harden at 830 to 870 degrees, then cool in oil or polymer bath. After hardening, slowly heat to tempering temperature.
If you wish, we can cut your steel to the desired fixed length with our high-performance band saws. In this way, a homogeneous structure is already created at the edge.
Material 1.2311 is available, for example, as sawn flat steel or round bar.
Do you have any questions about the material or would you like to order? Complete our inquiry form, it`s free of charge and without obligation. We will get in touch with you in order to provide you with more information.
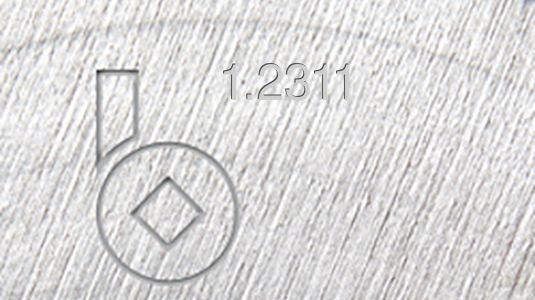
Standards
Material Category: Cold work tool steel
Applications
Injection molds, mold frames, base plates, die inserts and die holders
Heat Treatment
Hot forming 850 - 1050 C°
Stress relieving 580 - 600 C°
hardening 830 - 870 C° , cooling oil
hardening 830 - 870 C° , hot forming 180 - 220 C°
Tempering 500 - 650 C°
Chemical Composition
C % | Si % | Mn % | P % | S % | Cr % | Mo % |
0,35 -0,45 | 0,20 - 0,40 | 1,30 - 1,60 | max 0,035 | max 0,035 | 1,80 - 2,10 | 0,15 - 0,25 |
Mechanical Properties
Gerbrauchsfestigkeit | 930 - 1470 N/mm2 |
geglüht | <= 230 HB 30 |
gehärtet | Zugfestigkeit ~ 1170 N/mm² ~ 51 HRC |
angelassen bei ~ 100 C° | ~ 51 HRC |
angelassen bei ~ 200 C° | ~ 50 HRC |
angelassen bei ~ 300 C° | ~ 48 HRC |
angelassen bei ~ 400 C° | ~ 46 HRC |
angelassen bei ~ 450 C° | Zugfestigkeit ~ 1570 N/mm² |
angelassen bei ~ 500 C° | Zugfestigkeit ~ 1470 N/mm² ~ 42 HRC |
angelassen bei ~ 550 C° | Zugfestigkeit ~ 1320 N/mm² |
angelassen bei ~ 600 C° | Zugfestigkeit ~ 1180 N/mm² |
angelassen bei ~ 650 C° | Zugfestigkeit ~ 1030 N/mm² |
Material request